Navigating the dynamic market of shuttering props can be an intricate endeavor for those involved in construction projects. Shuttering props, vital for supporting slabs, beams, and other concrete forms during construction, have varying prices influenced by several factors. Understanding these pricing variables can equip professionals with the knowledge to make informed purchasing decisions.
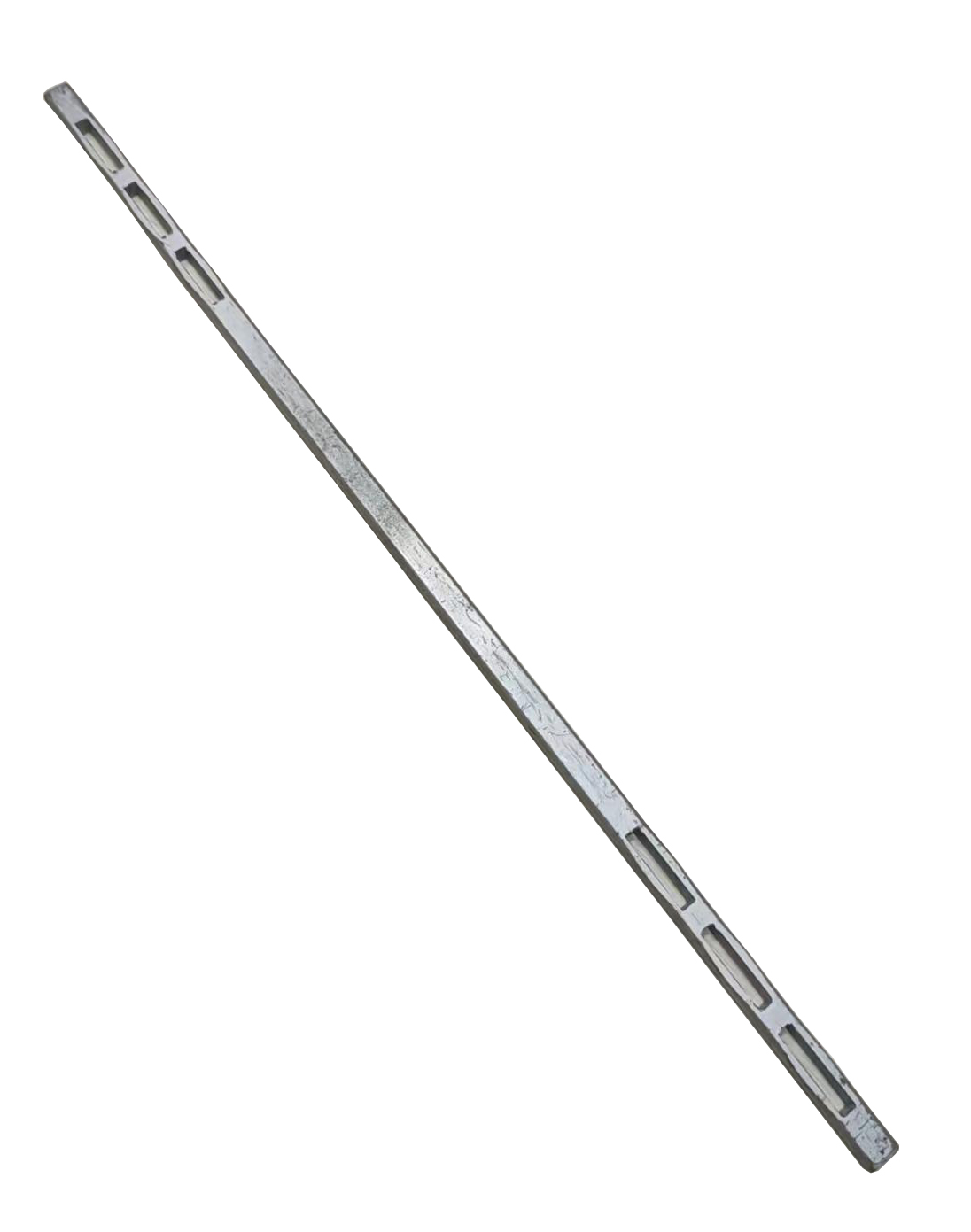
Shuttering props, essential in providing temporary support, vary in price based on material, quality, height, load capacity, and brand reputation. Typically, they are made from steel or aluminum, with steel options often being more economical but heavier, while aluminum props offer lighter alternatives at a higher cost due to their durability and ease of handling.
The quality of shuttering props is paramount, directly influencing price. High-grade props, designed to withstand construction rigors, tend to be priced higher. These props boast superior safety features, extended lifespans, and compliance with industry standards. Investing in reputable brands that emphasize quality assurance is crucial for reducing potential on-site failures, however, this often results in higher upfront costs.
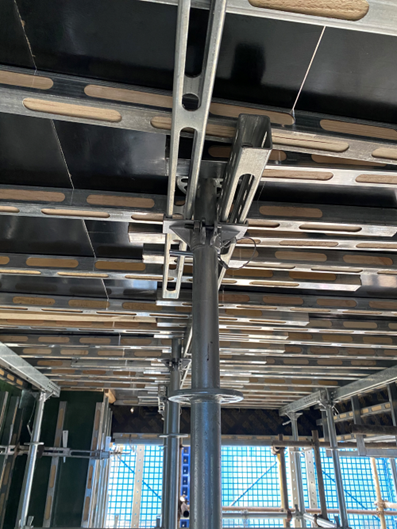
The height and adjustable range of props are significant pricing determinants. Props suitable for varied construction requirements offer extensive adjustability, allowing for multiple reuse across different project phases. These versatile props, while beneficial in saving costs over time, typically carry a higher initial price.
Load capacity is a crucial factor when considering prop prices. Higher load-bearing props, suitable for extensive construction, are generally more expensive due to enhanced structural integrity, supplying reliability for supporting heavy frameworks. It is vital to select props matching your specific project requirements to ensure cost-effectiveness and safety.
shuttering props price
Brand reputation and market presence also influence shuttering prop prices. Established brands, recognized for durability and after-sales support, tend to command higher prices. The added security of purchasing from well-known manufacturers often compensates for the added cost through reliability and trustworthiness.
When searching for cost-effective shuttering props, procurement strategies should include bulk purchasing, leasing options, or exploring certified pre-owned props as viable alternatives. Bulk purchasing often attracts discounted rates, while leasing offers flexibility without substantial capital investment. Pre-owned props, evaluated for safety and performance, provide an economical option without compromising quality.
Comparative market analysis and vendor negotiations can provide insight into competitive pricing. It is imperative to consider total ownership costs, including maintenance, transportation, and after-sales service, when calculating potential savings.
Navigating shuttering props’ complex pricing landscape requires attention to material, quality, size, brand reputation, and market strategies. This knowledge empowers professionals to make sound investment decisions, ensuring not only financial practicality but also the unwavering safety and success of their construction projects.