Understanding the Dynamics of Roof Shuttering Prices An Insider's Perspective
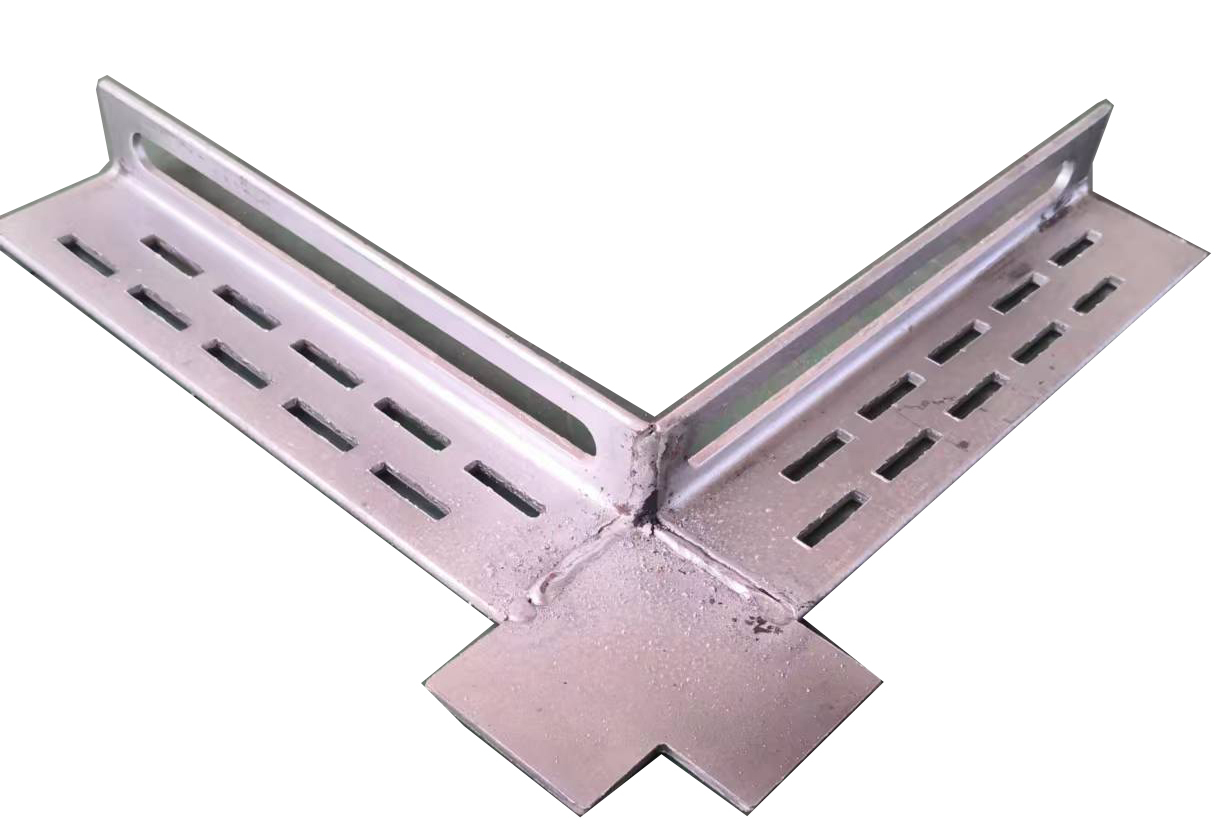
The construction industry, a crucial backbone of global infrastructure development, demands precise calculations and foresight, particularly when it comes to cost management. Among the various elements dictating the budget, roof shuttering plays a pivotal role. While it may appear to be just a fraction of the overall process, failure to accurately calculate the roof shuttering price can derail a project’s financial planning. This exploration delves into the complexities of roof shuttering costs, offering insights drawn from industry expertise and real-world experience.
Roof shuttering, a temporary mold used to support wet concrete until it cures and can support itself, is not a one-size-fits-all solution. The cost is influenced by multiple factors, such as the materials used, labor, design complexity, and geographical location. Understanding these aspects not only requires practical experience but also a grasp of the technical specifications that construction projects demand.
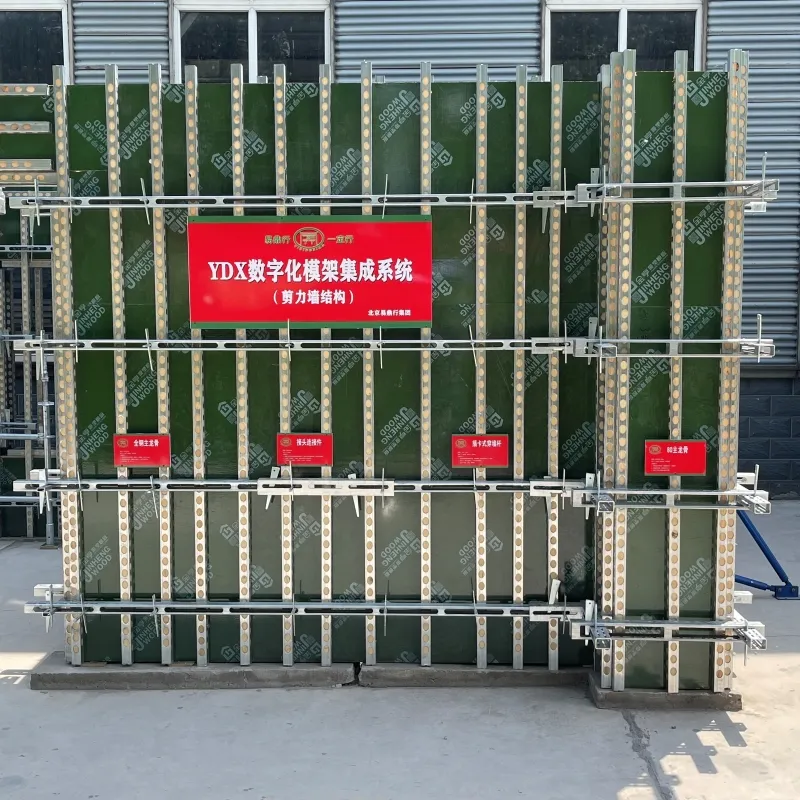
Material choice is one of the primary factors affecting cost. Traditionally, plywood and steel are the two most common materials used. Plywood is favored for its flexibility and cost-effectiveness, making it suitable for smaller projects or non-repetitive tasks. Conversely, steel, while initially costlier, offers durability and reuse potential, making it economical for large-scale or repetitive projects. Hence, an expert should evaluate the project scale and expected frequency of shuttering use to determine the most cost-effective material.
The complexity and design of the roof also significantly influence shuttering costs. Intricate designs requiring specialized forms or precise curvature demand more labor and time, escalating expenses. Experience emphasizes that detailed planning in the design phase, including consultations with engineers and architects, can lead to innovative solutions that reduce complexity without sacrificing quality or safety. Design simplification strategies, such as modular shuttering systems, can also provide cost benefits by streamlining operations and minimizing waste.
roof shuttering price
Labor costs, often an overlooked element, are another critical factor. Employing skilled and experienced personnel can initially appear expensive; however, their efficiency and proficiency can prevent costly errors and delays, resulting in overall savings. Real-world case studies consistently show that teams with a higher level of expertise produce better quality work within shorter timeframes, decreasing total project costs. Thus, investment in skilled labor is not just advisable but essential for maintaining cost efficiency.
Location also plays a vital role in determining roof shuttering costs. Local regulations, availability of materials, and labor costs can vary significantly between regions, impacting overall pricing. For instance, remote locations may incur additional transportation costs for materials and labor, thus increasing the shuttering price. A thorough understanding of local market conditions, facilitated by authoritative research and networking with local suppliers, can provide accurate pricing estimates and logistical solutions to mitigate these variations.
Authoritatively analyzing market trends can also offer insights into optimal purchasing times for materials and hiring labor. Price fluctuations due to economic conditions, seasonal demand variations, and technological advancements can influence costs. Building trustworthy relationships with suppliers and staying informed of market developments ensures a competitive edge in cost management.
Sustainable practices are increasingly influencing costs and preferences in modern construction. Eco-friendly materials, while slightly more expensive initially, may benefit from governmental incentives and offer longer-term savings due to their efficiency and reduced environmental impact. Staying informed on sustainable practices and their cost implications not only promotes environmental responsibility but can also enhance the project’s market appeal.
In conclusion, calculating roof shuttering price is an intricate process that requires balancing multiple dynamic factors. Through the lens of experience and expertise, understanding these variables allows for more accurate budgeting and efficient resource allocation. Authoritative knowledge and trustworthiness in handling these aspects not only ensure financial prudence but also elevate the quality and sustainability of the construction project.