When it comes to constructing structurally sound buildings, the lintel beam plays a crucial role in distributing loads from walls and roofs, particularly above openings like doors and windows. It's no secret among builders and architects that precise lintel beam shuttering is vital to achieving a successful and stable structure. Drawing from extensive industry expertise, this article delves into the intricacies of lintel beam shuttering, offering authoritative insights and trustworthy guidance for both seasoned professionals and those newer to the field.
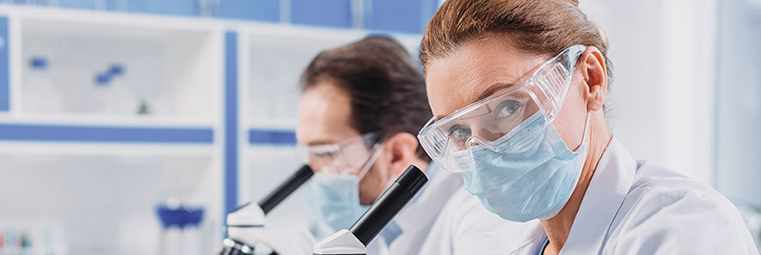
Experience and Expertise in Lintel Beam Shuttering
Shuttering, or formwork, for a lintel beam requires a deep understanding of its structural purpose and its role within the building's framework. The shuttering process starts by accurately designing the formwork, which serves as a mold for concrete, ensuring it sets into the intended shape and dimensions. Precision is key any deviation can compromise the integrity of the entire building structure. Therefore, employing professional-grade materials such as steel or high-density plywood for the formwork is recommended to withstand the pressure of poured concrete without deformation.
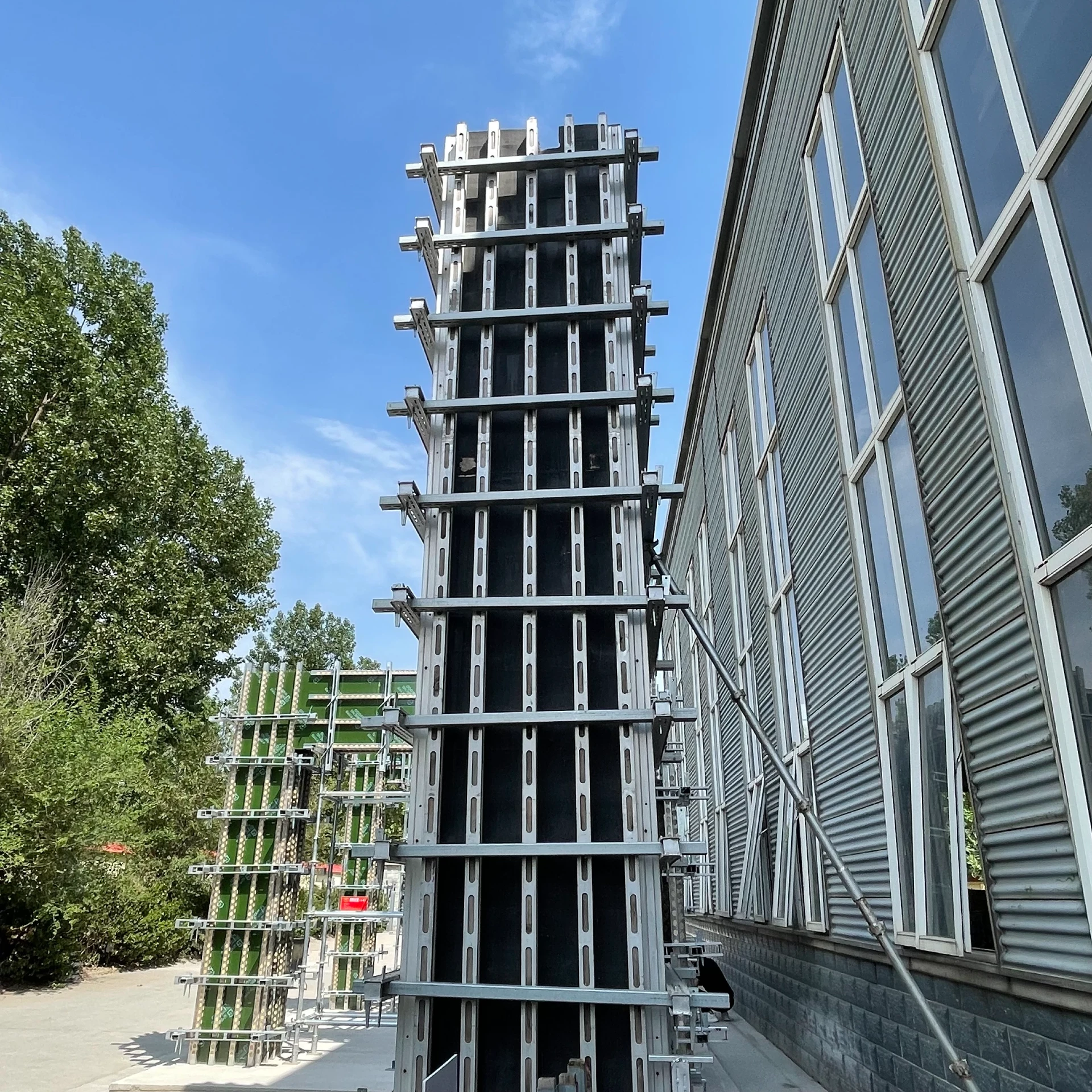
Field experts emphasize the importance of calibration and measurement. It’s not uncommon to see even seasoned professionals using laser levels and high-precision measuring tapes to ensure the formwork is aligned perfectly. Furthermore, correct bracing and support must be used to prevent sagging or displacement, especially under the weight of the wet concrete.
Authoritativeness in Techniques and Tools
Through authoritative insights gathered from leading construction engineers and architects, one critical aspect stands out the method of supporting the shuttering. Proper use of adjustable props and a well-organized staging system ensures that the formwork remains stable during the curing process. Experienced professionals often recommend regularly checking the props and fasteners during the casting process to avoid any unexpected shifts.
Moreover, advances in shuttering technology have introduced modular systems that improve ease of assembly and disassembly, ultimately saving time and cost on labor. Utilizing these systems not only enhances efficiency but provides a reliable framework that guarantees repeatability and uniformity across multiple lintel beams within a project.
lintel beam shuttering
Trustworthiness in Materials and Process
Trustworthy execution of lintel beam shuttering relies heavily on the quality of both materials and workmanship. The right choice of concrete mixture and its curing time are pivotal to achieving the necessary strength and durability. Adding to this foundation of trust, on-site engineers must conduct stringent checks on the formwork setup, including verifying the tightness of joints and ensuring there are no potential leak points for the concrete.
It is advisable to keep a detailed checklist during the formwork process, documenting every stage from setup to removal. This practice not only enhances accountability and transparency but also serves as an excellent resource for addressing any future issues that may arise.
Furthermore, working with certified industry professionals and manufacturers for supplies ensures top-grade materials are used, maintaining the trust clients place in construction companies to deliver safe and high-quality structures.
Innovative Approaches for Modern Projects
In the quest for modernization and efficiency, construction experts are increasingly adopting innovative shuttering methods like self-compacting concrete and digitally designed formwork.
These approaches minimize labor intensity and enhance precision. Digital modeling software allows the creation of highly accurate formwork plans, predicting potential issues before they occur on the construction site.
In conclusion, mastering lintel beam shuttering involves a blend of traditional know-how and modern advancements. By integrating experience with authoritative techniques and trustworthy materials, construction professionals ensure the engineering of safe, long-lasting, and efficient structures. Embracing these practices not only supports a project’s structural soundness but also builds confidence with clients, securing a reputation for excellence in the industry.